- Dobór, montaż i rola zespołu przygotowania powietrza dla narzędzi pneumatycznych
Dobór, montaż i rola zespołu przygotowania powietrza dla narzędzi pneumatycznych
Aby osiągnąć wysoki poziom wydajności narzędzi zasilanych sprężonym powietrzem, należy w pierwszej kolejności zadbać o optymalizację instalacji pneumatycznej. Warto w tym celu zwrócić uwagę na układy przygotowania sprężonego powietrza, które w swej strukturze składają się z filtra ciśnieniowego, reduktora ciśnienia oraz naolejacza. Elementy te mają realny wpływ na efektywność i wytrzymałość w długim okresie narzędzi oraz innych urządzeń pneumatycznych. Zainstalowanie zespołu przygotowania sprężonego powietrza w okolicy narzędzia pneumatycznego zagwarantuje właściwą jakość sprężonego powietrza, bowiem zniweluje poziom ryzyka związanego z obecnością w instalacji pyłu, wilgoci, rdzy oraz innych zanieczyszczeń stałych. Naolejacz mgły olejowej znajdujący się w zespole F+R+L zapewnia także właściwe smarowanie narzędzia.
W artykule znajdziesz odpowiedzi na pytania:
Dlaczego zespół przygotowania sprężonego powietrza jest tak ważny dla narzędzi pneumatycznych?
Jaką rolę dla narzędzi odgrywa smarowanie, filtracja i regulacja ciśnieniem?
Jak zamontować i dobrać blok przygotowania powietrza?
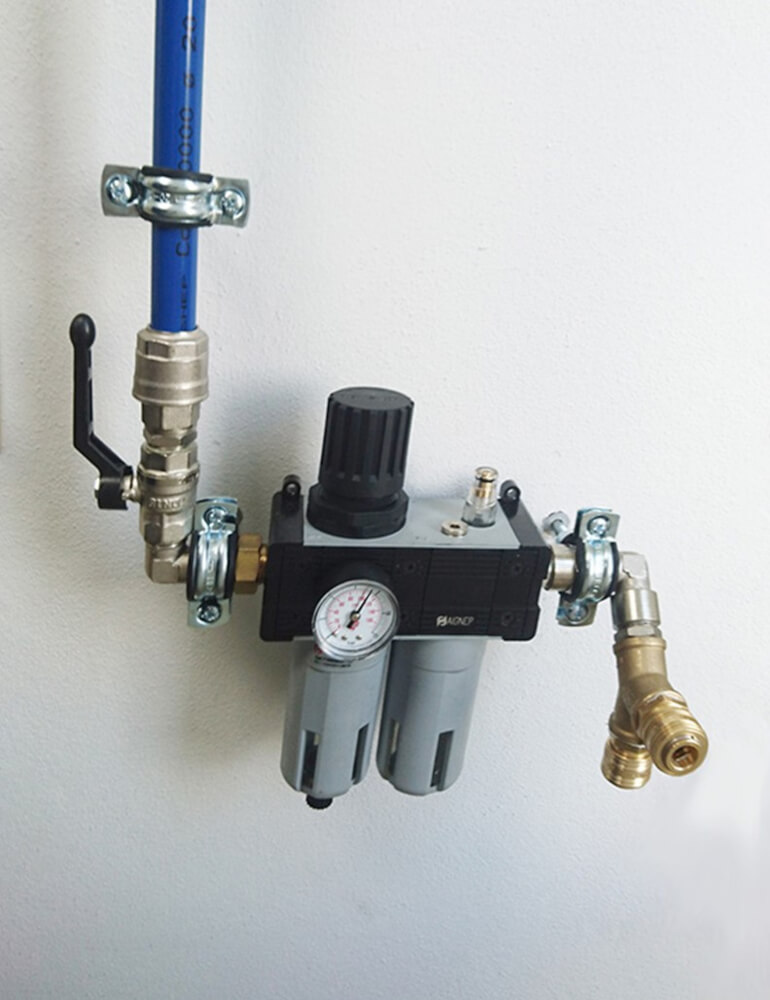
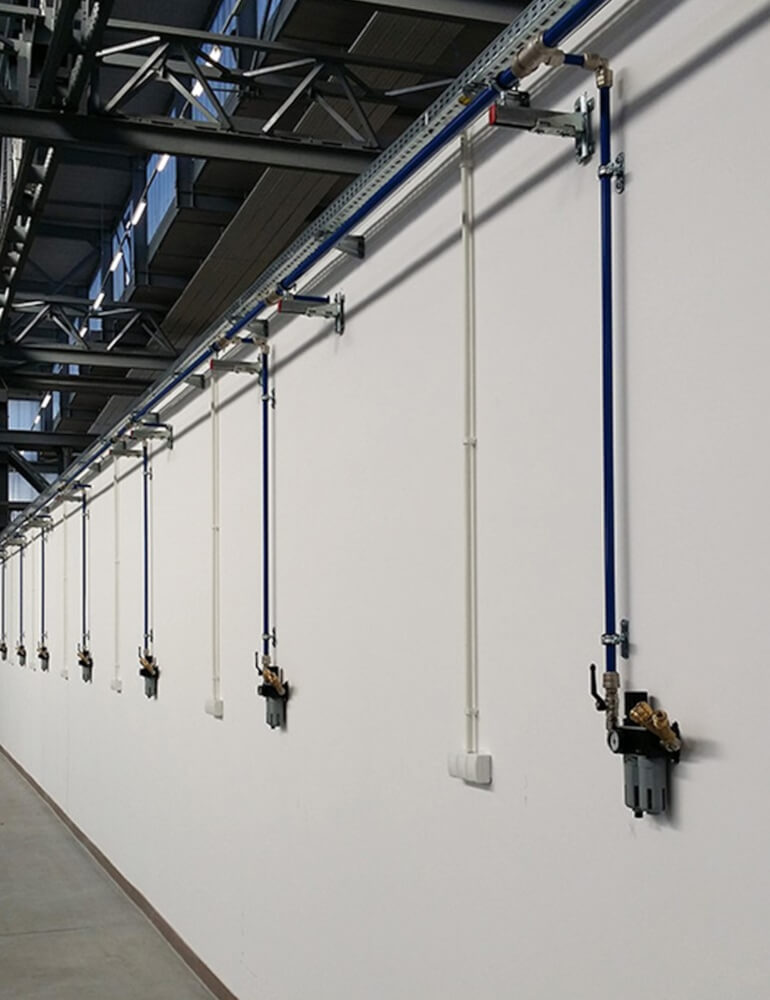
Blok sprężonego powietrza charakteryzuje się następującymi działaniami: filtrowaniem, regulacją (redukcją) ciśnienia i smarowaniem
Filtrowanie – proces polegający na zastosowaniu filtra powietrznego, który eleminuje ze sprężonego większość zanieczyszczeń w postaci cząstek stałych pyłu, rdzy itp. Jeśli cząstki pyłu, rdzy lub innych zanieczyszczeń dostaną się do silnika pneumatycznego lub narzędzia mogą utrudniać przepływ medium, a tym samym przyczyniać się do straty mocy samego sprzętu oraz powodować jego uszkodzenia. Powoduje to wyższe kosztu serwisu oraz zwiększony pobór sprężonego powietrza np. w wyniku wycieków i uszkodzeń uszczelnień w urządzeniach pneumatycznych.
Smarowanie – proces polegający na dawkowaniu do powietrza przepływającego pod ciśnieniem kropel oleju które zamieniane są w mgłę olejową. W momencie, gdy nie zachodzi czynność smarowania, proces zużycia narzędzia jest zdecydowanie szybszy, co wiąże się także ze spadkiem maksymalnej wydajności szlifierki, młotka, wiertarki czy wkrętaka. Ma to przełożenie na obniżenie produktywności całej pracy jak i produkcji ogółem, podnoszą się jednocześnie koszty serwisowe. Zachęcamy do zapoznania się z wykresem poniżej, na którym pokazaliśmy parametry wydajności / trwałości użytkowej motoreduktora pneumatycznego w przypadku zastosowania smarowania i jego braku.
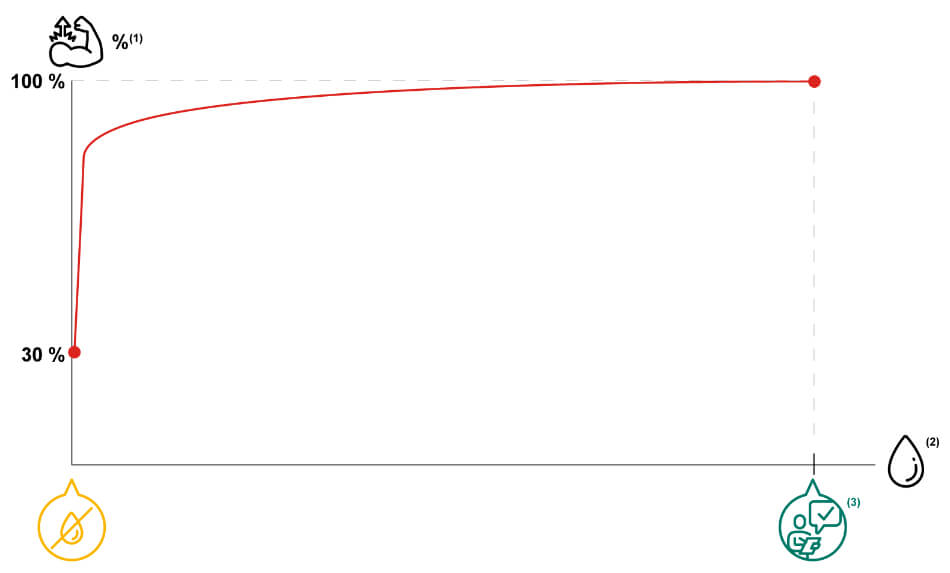
Wykres nr. 1: W pełni pożądane działanie motoreduktora pneumatycznego w narzędziu przy zachowaniu właściwego smarowania. Wykorzystano parametry przykładowe, na bazie testów w laboratorium, gdzie wykonany próby na motoreduktorach pneumatycznych. Wartość 1 to moc wyjściowa silnika narzędzia, z kolei numer 2 oznacza wolumen olejowy, a 3 dotyczą zaleceń producenckich z tzw. karty DTR (instrukcja obsługi dołączana do każdego narzędzia).
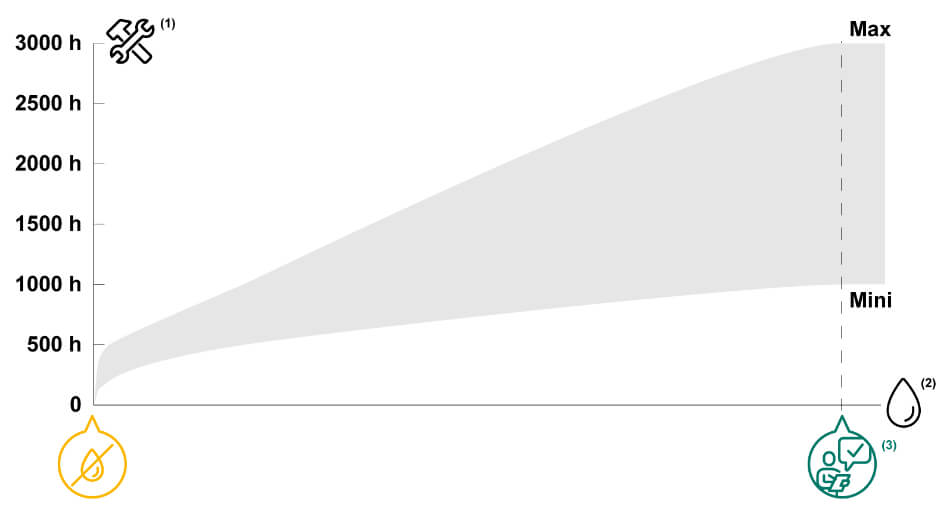
Wykres nr. 2: W pełni pożądana wytrzymałość użytkowa motoreduktora pneumatycznego danego narzędzia przy odpowiednim smarowaniu mgłą olejową. Wykorzystano parametry przykładowe, bazujące na testach wykonanych w laboratorium na motoreduktorach pneumatycznych. Numer 1 dotyczy mocy wyjściowej silnika narzędzia, 2 to wolumen ilościowy oleju, 3 to zalecenia wynikające z karty DTR produktu (dołączona karta katalogowa z instrukcją obsługi).
Regulowanie - proces redukcji ciśnieniowej, który pomaga utrzymać ciśnienie dynamiczne na kontrolowanym poziomie 90 psi / 6,3 bar. Jest to bardzo istotne, bowiem ciśnienie na mniejszym poziomie niż wskazane przez producenta narzędzi wpływa na obniżenie wydajności jego pracy, a tym samym spada rentowność procesu, inwestycji. Jeśli jednak ciśnienie przekroczy wymaganą wartość, może to prowadzić do jego szybszego wyeksploatowania. Może być to także skutkiem usterek, wypadków czy doprowadzić do awarii całego układu pneumatycznego w zakładzie.
Jak wybrać zespół przygotowania powietrza?
Podczas doboru bloku przygotowania sprężonego powietrza należy przede wszystkim wziąć pod uwagę, wielkość gwintu przyłączeniowego oraz wymagania narzędzi dotyczących przepływu powietrza i stopnia filtracji powietrza.
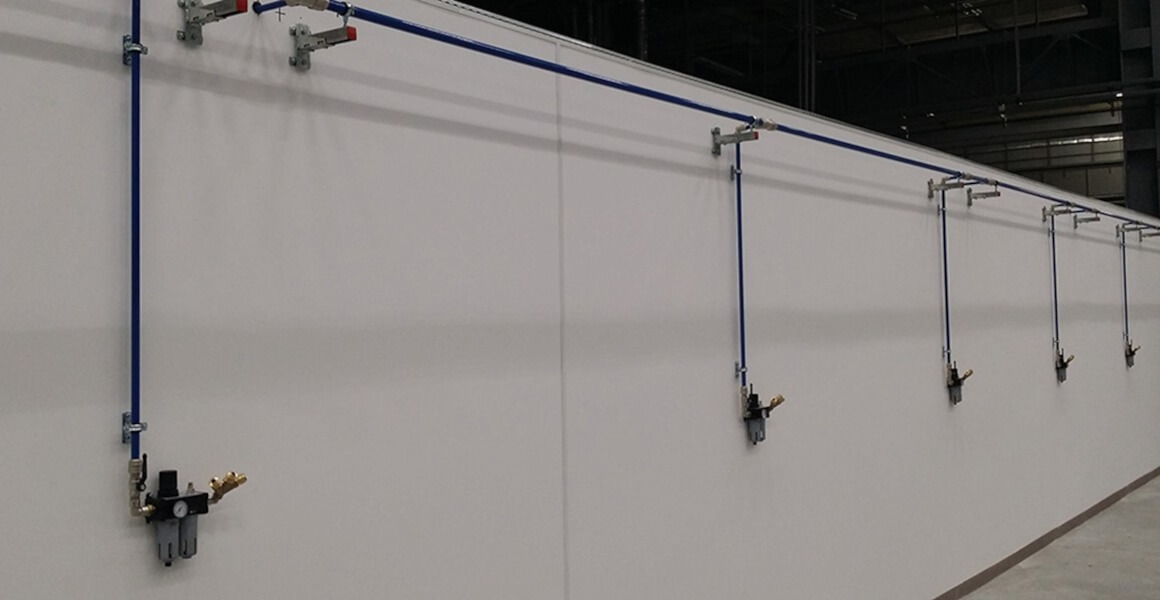
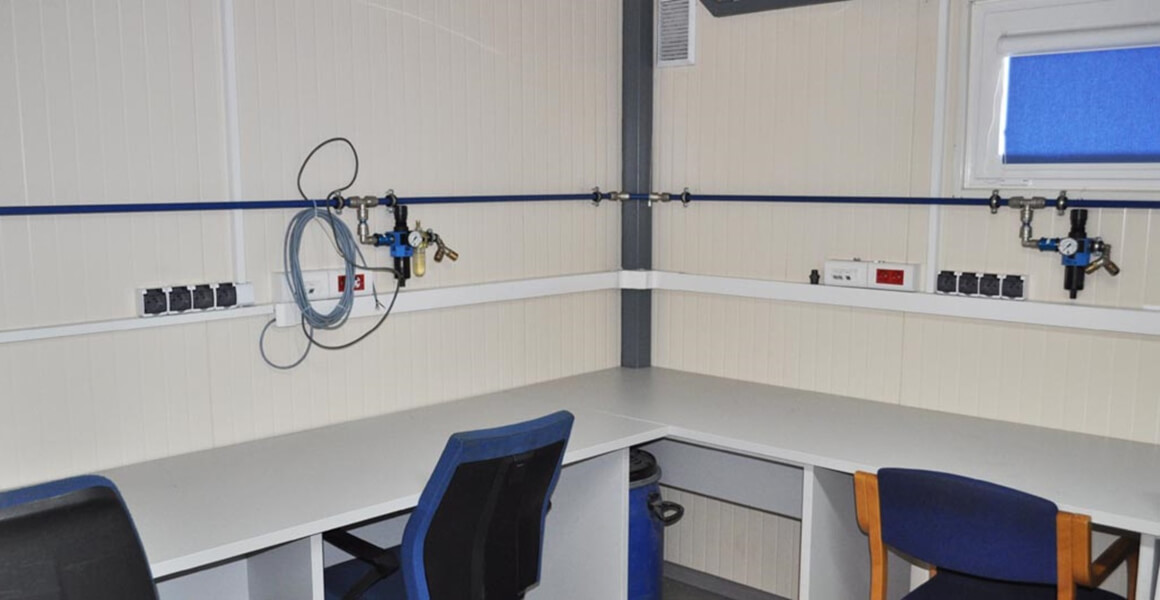
Jak powinniśmy zamontować takie bloki przygotowania sprężonego powietrza?
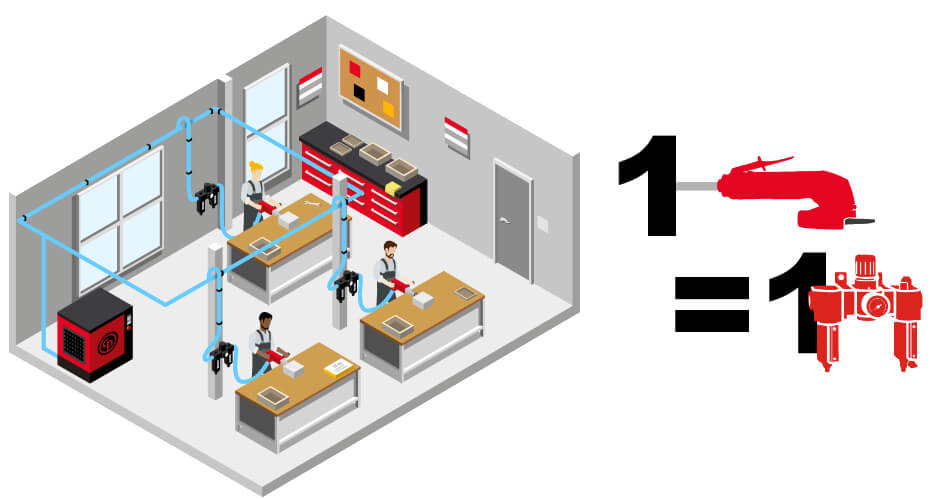
Co ciekawe i jednocześnie warte pokreślenia, w zdecydowanej większości narzędzia pneumatyczne nie pracują na maksymalnych obrotach, a przyczyną tego jest nieprawidłowe przygotowanie sprężonego powietrza w układzie. Mowa tutaj o całej instalacji pneumatycznej w fabryce czy warsztacie, dlatego też zaleca się przestrzeganie reguł takich jak:
Stosowanie 1 stacja przygotowania powietrza na 1 narzędzie pneumatyczne. W momencie, kiedy podłączymy kilka narzędzi pneumatycznych do jednego bloku powietrza, to wielkość ciśnienia powietrza jak i produktywność naolejania obniżą się,
Zespół przygotowania sprężone powietrza powinno się zainstalować w jak najbliższej odległości od narzędzia, dokładnie w takim miejscu, gdzie wąż zasilający odbiornik jest zamontowany do instalacji, tak aby do danego narzędzia dochodziła mgiełka olejowa i jednocześnie nie występował spadek ciśnienia,
Przed każdym zastosowaniem klucza, szlifierki czy wiertarki należy mieć pewność, że stan oleju jest prawidłowy, gdyż proces smarowania pozytywnie wpływa na wytrzymałość narzędzi,
Wkłady filtracyjne należy cyklicznie sprawdzać i wymieniać.
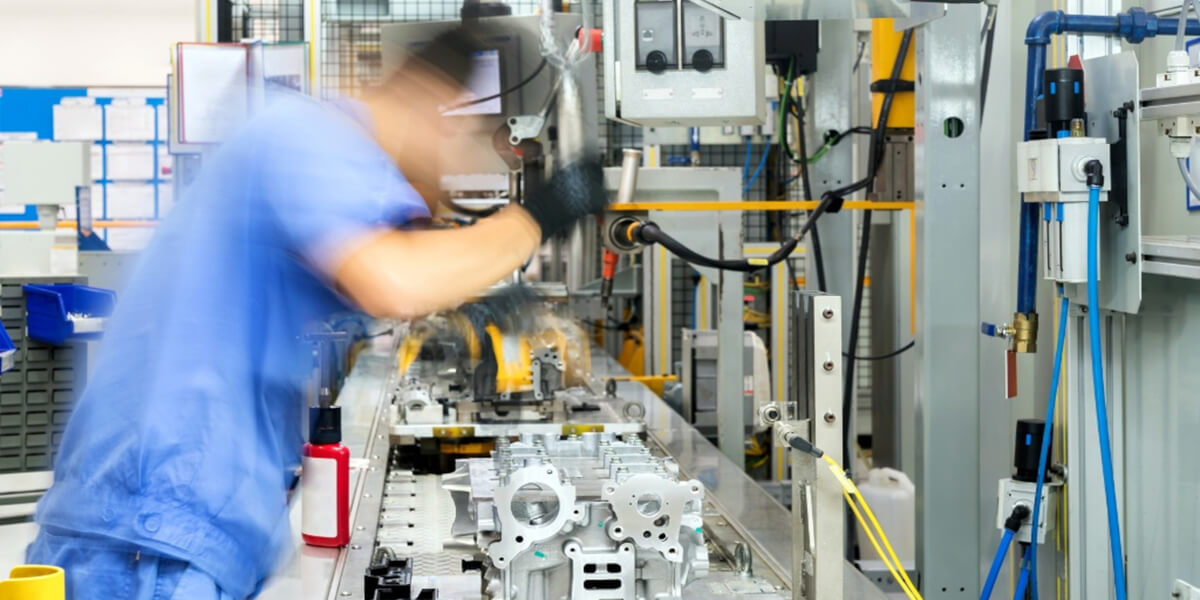
Podsumowując, narzędzia zasilane sprężonym powietrzem, dedykowane są pracy przy dynamicznych wartościach ciśnienia powietrza 90 PSI/ 6,3 bar i podlegają systematycznemu smarowaniu. Większy poziom ciśnienia wpłynie negatywnie na wytrzymałość samego narzędzia jak i bezpieczeństwa osoby pracującej z narzędziem. Wysokie ciśnienie to także większy poziom wibracji, zbyt wysoka prędkość obrotowa, która ma przełożenie na intensywniejsze tarcie jak i stwarza możliwość uszkodzenia.
2022-12-08
Pneumat.
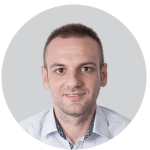
Autor:
Rafał Ruminiak
Product Manager
Armatura Przemysłowa
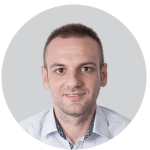
Autor:
Rafał Ruminiak
Product Manager
Armatura Przemysłowea
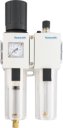
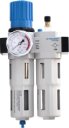
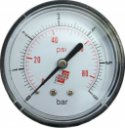
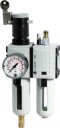
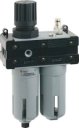