Osprzęt do chwytaków
- Produkty
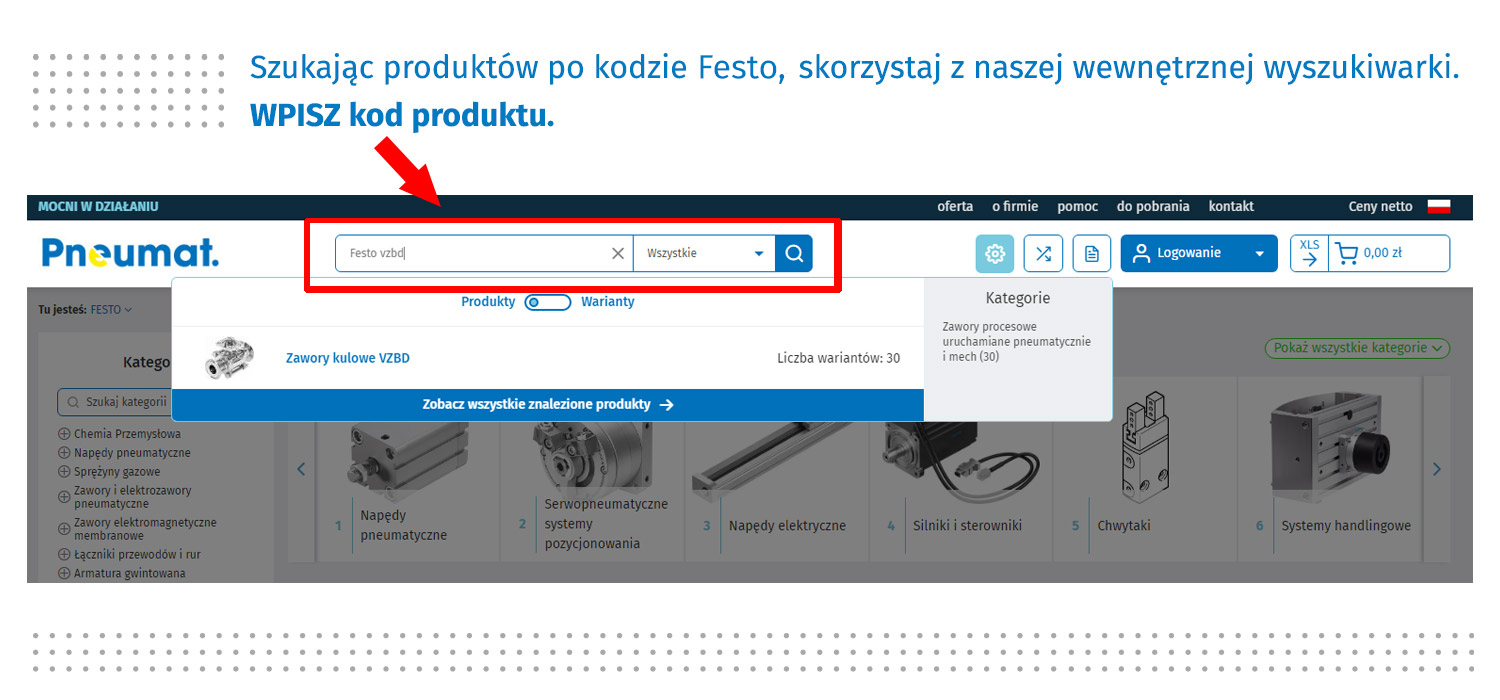
Faq - Osprzęt do chwytaków Festo - Najczęściej zadawane pytania
Membrana chwytaka DHAS jest kluczowym komponentem w chwytakach pneumatycznych Festo, służącym do tworzenia dynamicznego uszczelnienia między ruchomymi a nieruchomymi częściami chwytaka. Umożliwia to:
zachowanie ciśnienia pneumatycznego niezbędnego do działania chwytaka
absorpcję wibracji i udarów, co zapewnia większą trwałość i niezawodność chwytaka
zapewnienie płynności ruchu chwytaka poprzez minimalizację tarcia między komponentami
Zestawy montażowe DHAS są zaprojektowane, aby ułatwić instalację i zwiększyć funkcjonalność chwytaków pneumatycznych Festo. Ich główne zalety to:
modułowa konstrukcja, która pozwala na szybką i łatwą instalację oraz wymianę chwytaków bez potrzeby demontażu całego systemu.
wysoka kompatybilność z różnymi modelami chwytaków, co umożliwia elastyczne dostosowanie systemu do specyficznych wymagań aplikacji.
zwiększona precyzja montażu, co minimalizuje ryzyko błędów operacyjnych i poprawia ogólną wydajność systemu.
Szczęki adaptacyjne do chwytania DHAS są specjalnie zaprojektowane do obsługi różnorodnych kształtów i materiałów, co czyni je idealnymi do zastosowań wymagających wysokiej elastyczności, takich jak:
automatyczne linie montażowe, gdzie różne produkty wymagają indywidualnych ustawień chwytaków
zastosowania z szybkimi zmianami produkcji, gdzie czas przejścia między seriami produktów musi być minimalny
precyzyjne manipulacje, gdzie delikatne lub nieregularnie kształtowane przedmioty wymagają indywidualnie dostosowanych uchwytów
Zespoły adapterów dla chwytaków umożliwiają ich łatwą adaptację do różnych zadań w automatyce przemysłowej. Ich główne korzyści to:
uniwersalność zastosowań, dzięki możliwości szybkiej zmiany chwytaków lub dopasowania ich do specyficznych zadań
zwiększona efektywność operacyjna, poprzez redukcję czasu potrzebnego na konfigurację i zmiany w linii produkcyjnej
poprawa trwałości systemu, dzięki ochronie chwytaków przed nadmiernym zużyciem poprzez równomierne rozłożenie obciążeń operacyjnych
Szczęki chwytaka oferowane jako półfabrykaty pozwalają użytkownikom na ich samodzielne dopracowanie i dostosowanie do konkretnych zastosowań. Proces dostosowania może obejmować:
obróbkę mechaniczną, taką jak cięcie, szlifowanie czy frezowanie, aby uzyskać wymagane wymiary i kształty
dodawanie powłok ochronnych lub specjalistycznych materiałów zwiększających przyczepność
integrację z sensorami do monitorowania siły chwytu i obecności chwytanego obiektu
Redukcja skoku w chwytakach ma kluczowe znaczenie w aplikacjach, gdzie wymagana jest duża precyzja i delikatność manipulacji, takich jak:
mikromontaż, gdzie nawet minimalne nadmierne ruchy mogą spowodować uszkodzenie delikatnych komponentów
operacje wymagające wysokiej precyzji, takie jak składanie elektroniki czy precyzyjna mechanika
zastosowania w biotechnologii i farmacji, gdzie niezawodność i precyzja są krytyczne dla bezpieczeństwa i skuteczności produktów
Technologie wykorzystywane w osprzęcie do rozpoznawania położenia obejmują przede wszystkim sensory optyczne, magnetyczne i indukcyjne, które oferują:
wysoką dokładność pomiaru, niezbędną w aplikacjach wymagających precyzyjnego pozycjonowania
szybką odpowiedź, co jest kluczowe w szybko działających systemach automatyzacji
możliwość integracji z systemami sterowania, co pozwala na automatyczne korygowanie parametrów pracy w czasie rzeczywistym
Osprzęt do chwytaków wspomaga zwiększenie wydajności produkcji przez:
automatyzację procesów chwytania, co redukuje czas cyklu operacji i zmniejsza potrzebę interwencji ludzkiej
zwiększenie niezawodności i powtarzalności operacji, dzięki precyzyjnemu wykonaniu i wysokiej jakości komponentów
elastyczność w adaptacji do różnych produktów, co pozwala na szybką rekonfigurację linii produkcyjnych w odpowiedzi na zmiany asortymentu
Główne wyzwania w utrzymaniu osprzętu do chwytaków obejmują:
zużycie mechaniczne, które można minimalizować przez regularne inspekcje i wymianę zużytych komponentów
akumulacja zanieczyszczeń, zwłaszcza w środowiskach o wysokiej zawartości pyłów lub olejów, co wymaga częstszego czyszczenia i stosowania odpowiednich uszczelnień
potrzeba regularnej kalibracji, aby zapewnić, że systemy chwytające działają z oczekiwaną precyzją
Festo ciągle modernizuje technologicznie osprzęt do chwytaków, aby lepiej sprostać wymaganiom Przemysłu 4.0, wprowadzając:
inteligentne sensory, które monitorują stan chwytaków i automatycznie dostosowują parametry pracy dla optymalnej wydajności
systemy komunikacji bezprzewodowej, które pozwalają na zdalne sterowanie i diagnostykę chwytaków
moduły AI, które analizują dane operacyjne w czasie rzeczywistym, przewidują potrzeby konserwacyjne i optymalizują parametry pracy na bieżąco
Integracja osprzętu do chwytaków z systemami automatyki może być realizowana przez:
wykorzystanie standardowych interfejsów komunikacyjnych, takich jak IO-Link, Ethernet/IP, które są wspierane przez większość nowoczesnych systemów sterowania
programowanie współpracy między chwytakami a innymi elementami linii produkcyjnej przez zaawansowane oprogramowanie PLC lub dedykowane oprogramowanie Festo
stosowanie modułów adapterów, które fizycznie i elektrycznie integrują chwytaki z różnymi typami maszyn i robotów
Dla wyboru szczęk chwytaka jako półfabrykatu, najlepsze praktyki obejmują:
analizę wymagań aplikacji, w tym rozmiaru, kształtu, i materiału obiektów do manipulacji
wybór materiałów i technologii produkcji szczęk, które najlepiej odpowiadają specyficznym wymaganiom trwałości, elastyczności i przyczepności
testowanie prototypów szczęk, aby upewnić się, że spełniają one wszystkie wymagania operacyjne przed pełną skalą produkcji
Zespoły adapterów w kontekście modułów HSP i HSW Festo pełnią kilka kluczowych funkcji:
umożliwienie szybkiej zmiany narzędzi roboczych bez potrzeby długotrwałych przerw w produkcji
adaptacja chwytaków do różnych zadań przez zmianę efektorów końcowych, szczęk, czy innego osprzętu
integracja z systemami sensorycznymi, która pozwala na lepsze monitorowanie i kontrolę procesów chwytania
Kluczowe aspekty konserwacji szczęk chwytaka obejmują:
regularne sprawdzanie stanu mechanicznego, w tym poszukiwanie oznak zużycia czy uszkodzeń
czyszczenie szczęk od resztek materiałów lub innych zanieczyszczeń, które mogłyby wpływać na ich funkcjonowanie
smarowanie ruchomych części, jeśli szczęki zawierają takie elementy, aby zapewnić płynność ruchów i minimalizować ryzyko zacięć
Redukcja skoku w chwytakach pozwala na bardziej precyzyjną kontrolę procesów produkcyjnych przez:
zmniejszenie czasu cyklu, jako że krótszy skok oznacza szybsze otwieranie i zamykanie chwytaka
poprawę dokładności pozycjonowania, co jest krytyczne w aplikacjach wymagających wysokiej precyzji, takich jak mikromontaż
zwiększenie trwałości urządzenia, ponieważ mniejsze ruchy mechaniczne redukują zużycie komponentów
Integracja technologii rozpoznawania położenia z chwytakami obejmuje:
zastosowanie sensorów położenia, takich jak enkodery liniowe czy czujniki halla, które dostarczają danych o dokładnej pozycji chwytaka w czasie rzeczywistym
wykorzystanie systemów wizyjnych, które mogą identyfikować położenie i orientację obiektów, umożliwiając chwytakom automatyczne dostosowanie parametrów chwytu
programowanie adaptacyjne, które pozwala chwytakom na samodzielne dostosowanie siły i pozycji chwytu w zależności od rozpoznanego obciążenia lub innych warunków operacyjnych
Osprzęt do rozpoznawania położenia znacząco redukuje błędy operacyjne poprzez:
automatyzację korekt, gdzie systemy automatycznie dostosowują parametry działania w odpowiedzi na błędy położenia wykryte przez sensory
zwiększenie precyzji montażu i manipulacji, co jest szczególnie ważne w precyzyjnych aplikacjach technologicznych
minimalizację przestojów i interwencji ludzkich, dzięki ciągłemu i niezawodnemu monitorowaniu stanu maszyny
Przyszłe kierunki rozwoju osprzętu do chwytaków mogą obejmować:
rozwój inteligentnych chwytaków, które będą wyposażone w zaawansowane algorytmy AI do samodzielnej adaptacji i optymalizacji procesów
integracja z robotyką kolaboratywną, gdzie chwytaki będą bezpiecznie współpracować z ludźmi bez potrzeby dodatkowych zabezpieczeń
wykorzystanie nowych materiałów i technologii, takich jak nanotechnologie czy zaawansowane polimery, które pozwolą na tworzenie bardziej wydajnych i trwałych chwytaków
Strategie te obejmują:
Regularne przeglądy i konserwacje, które powinny być planowane w oparciu o intensywność użytkowania i warunki środowiskowe.
Użycie wysokiej jakości komponentów z atestami i certyfikatami, które gwarantują ich trwałość i odporność na warunki przemysłowe.
Implementacja systemów monitorujących, które mogą w czasie rzeczywistym oceniać stan techniczny chwytaków i prognozować potrzeby serwisowe.
Integracja różnych rodzajów osprzętu do chwytaków wymaga:
Planowania kompatybilności, gdzie wszystkie komponenty muszą być dobrane pod kątem współpracy mechanicznej i elektrycznej.
Programowania zintegrowanego, które uwzględnia interakcje między różnymi elementami osprzętu, aby zapewnić płynną i efektywną operację.
Testowania systemowego, które pozwala zweryfikować, czy zintegrowany system spełnia wszystkie oczekiwania funkcjonalne i operacyjne.
Wybór odpowiedniej membrany dla chwytaków DHAS jest kluczowy z kilku powodów:
Materiał membrany - musi być odporny na środki chemiczne i temperaturę, jakie występują w środowisku pracy. Elastomery takie jak NBR czy silikon są często stosowane ze względu na ich elastyczność i odporność chemiczną.
Twardość membrany - wpływa na siłę chwytu i precyzję – miękkie membrany mogą lepiej dopasować się do nieregularnych powierzchni, ale mogą nie oferować wystarczającej siły chwytu dla cięższych obiektów.
Trwałość - membrana powinna wytrzymać warunki operacyjne bez pękania czy odkształceń, które mogłyby wpłynąć na jej funkcjonalność.
Instalacja zestawów montażowych DHAS wymaga ścisłego przestrzegania kilku kroków, aby zapewnić ich prawidłowe działanie:
precyzyjne dopasowanie - zestawy montażowe muszą być dokładnie dopasowane do chwytaków, aby uniknąć luźnych połączeń, które mogą prowadzić do awarii mechanicznych.
zachowanie czystości - podczas montażu, powierzchnie styku powinny być czyste i wolne od zanieczyszczeń, które mogłyby wpłynąć na stabilność montażu.
stosowanie odpowiednich narzędzi - użycie narzędzi zalecanych przez producenta zapewni, że elementy są montowane z właściwym momentem obrotowym, co jest kluczowe dla trwałości i bezpieczeństwa połączeń.
Szczęki adaptacyjne DHAS są projektowane tak, aby łatwo dostosować się do różnych przedmiotów, co jest kluczowe w dynamicznie zmieniających się warunkach produkcji:
modułowa konstrukcja - pozwala na szybką zmianę szczęk bez potrzeby wymiany całego chwytaka
automatyczne dostosowanie - niektóre modele mogą automatycznie dostosować siłę i rozmiar chwytu w zależności od rozmiarów i kształtu manipulowanego przedmiotu
wysoka kompatybilność - umożliwiają współpracę z różnorodnymi typami produktów bez konieczności przeprogramowania systemu czy dokonywania innych zmian konfiguracyjnych
Zespoły adapterów są nieocenione w konserwacji i przestawianiu linii produkcyjnych dzięki:
elastyczności konfiguracji - pozwalają na szybkie dostosowanie chwytaków i innych komponentów do zmieniających się wymagań produkcyjnych
minimalizacji czasu przestoju - szybka wymiana lub modyfikacja komponentów znacząco redukuje czas przestoju maszyn
redukcji kosztów - zmniejszenie potrzeby inwestycji w różnorodne specjalistyczne chwytaki, co obniża koszty operacyjne
Szczęki chwytaka oferowane jako półfabrykaty pozwalają użytkownikom na ich dokładne dostosowanie do indywidualnych potrzeb, co zwiększa adaptacyjność systemów chwytających:
indywidualne dostosowanie - możliwość obróbki końcowej szczęk do specyficznych wymiarów i kształtów
szybka reakcja na zmiany - umożliwiają szybką adaptację do nowych produktów lub zmienionych wymagań produkcyjnych
koszty - zazwyczaj niższe w porównaniu do kompletnie opracowanych, dedykowanych szczęk chwytakowych
Redukcja skoku w chwytakach pozwala na bardziej precyzyjne i delikatne manipulowanie przedmiotami, szczególnie przydatne w:
mikroasemblacjach - gdzie precyzyjne umiejscowienie jest krytyczne
operacjach z delikatnymi materiałami - minimalizuje ryzyko uszkodzenia przez ograniczenie nadmiernej siły chwytu
zwiększenie kontroli - pozwala operatorom na bardziej kontrolowane i subtelne operacje, idealne w precyzyjnym montażu
Wyzwania techniczne związane z integracją osprzętu do rozpoznawania położenia z chwytakami obejmują:
kompatybilność elektryczna i mechaniczna - zapewnienie, że osprzęt jest kompatybilny z istniejącymi systemami chwytaków, co może wymagać stosowania adapterów lub modyfikacji
złożoność konfiguracji - ustawienie i kalibracja sensorów może być czasochłonne, ale stosowanie prostych, użytkownikom przyjaznych interfejsów może to ułatwić
koszty - wyższe początkowe inwestycje mogą być barierą, którą można przezwyciężyć przez szkolenia dotyczące ROI i efektywności kosztowej
Najlepsze praktyki w utrzymaniu szczęk chwytaka obejmują:
regularne inspekcje - sprawdzanie szczęk pod kątem zużycia, pęknięć czy innych uszkodzeń
czyszczenie i smarowanie - regularne czyszczenie z zanieczyszczeń oraz stosowanie smaru, gdzie to konieczne, aby zapewnić płynność działania
wymiana w razie potrzeby - nie zwlekać z wymianą szczęk, które wykazują znaki znacznego zużycia, aby uniknąć przestojów produkcyjnych
Osprzęt do chwytaków może znacząco przyczynić się do poprawy ergonomii i bezpieczeństwa pracy przez:
zmniejszenie potrzeby interwencji ludzkiej - automatyzacja zadań redukuje potrzebę wykonywania monotonnych lub potencjalnie niebezpiecznych operacji przez pracowników
zapewnienie stałej jakości operacji - automatyczne systemy chwytające zapewniają powtarzalność i eliminują błędy ludzkie
bezpieczne projektowanie - osprzęt taki jak osłony czy czujniki bezpieczeństwa może zapobiegać wypadkom, chroniąc operatorów przed ruchomymi częściami maszyn
Technologia sensorowa w osprzęcie do chwytaków umożliwia zaawansowaną automatyzację przez:
precyzyjne rozpoznawanie położenia - sensory mogą dokładnie określić położenie przedmiotów, co jest niezbędne w precyzyjnym montażu i składaniu
automatyczne dostosowanie parametrów chwytu - na podstawie danych z sensorów, systemy mogą automatycznie regulować siłę i pozycję chwytu, zapewniając optymalne działanie
integracja z systemami kontroli - dane z sensorów mogą być używane do ciągłego doskonalenia procesów, poprzez analizę i optymalizację w czasie rzeczywistym